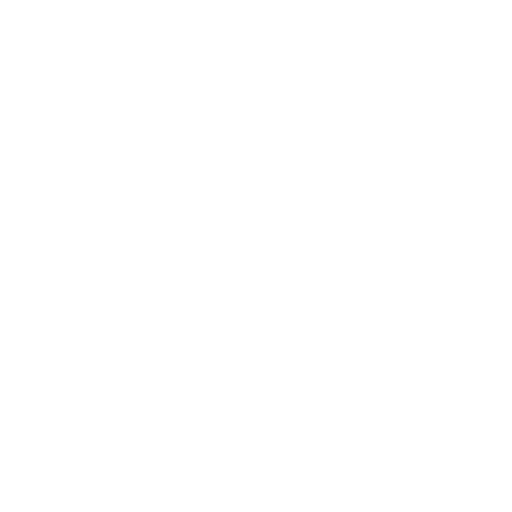
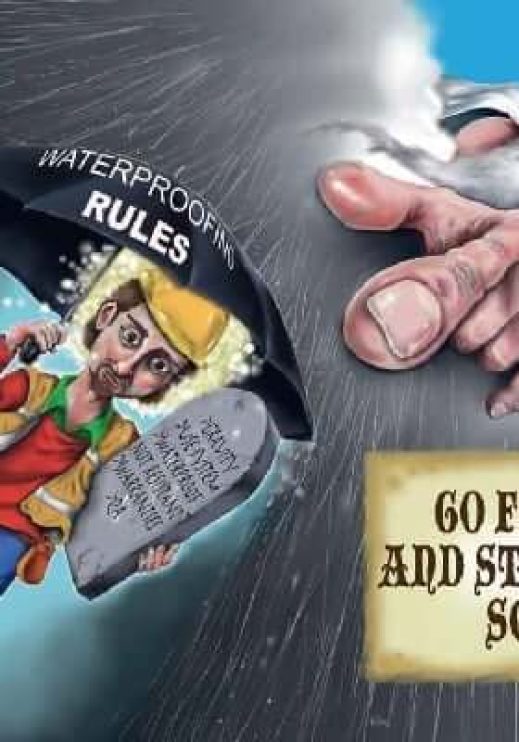
Waterproofing mistakes are arguably the most costly to everyone. Jerry Tyrrell provides the third in a series of articles that translate the National Construction Code (Building Code of Australia) into builder speak.
Back in 2005, one of the first articles I wrote for this column was on waterproofing – see ‘Avoid being a drip!’ This time I don’t intend to:
- Refer to the 120 plus pages of information in the National Construction Code (NCC) and associated Australian Standards.
- Discuss different membranes or examine the many different forms of the same detail.
The bottom line everyone wants is that “moisture does not penetrate or damage the waterproof system and the system will continue to perform for a minimum 50 years unless exposed to sunlight or a catastrophic event such as cyclone, earthquake or vandalism.”
Let’s apply the same principles and rules consistently. For instance, the 150mm turnup inside a shower is the same as turnup on your balcony. A bond breaker remains the same at ANY corner. Detailing over a joint between different substrates is the same whether you are inside a drained laundry or on a roof terrace.
THE SOURCE DOCUMENTS
- National Construction Code Volume 1 (pages 79-80 and 316-322).
- National Construction Code Volume 2 (pages 59-61 and 345-351).
- Australian Standard 3740-2010 Waterproofing of wet areas within residential buildings (38 pages).
- Australian Standard 4654.1-2012 Waterproofing membrane systems for exterior use – above ground level Part 1: Materials (18 pages).
- Australian Standard 4654.2-2009 Waterproofing membrane systems for exterior use – above ground level Part 2: Design and installation (32 pages).
COMMON SENSE
The basic RULES of waterproofing are common sense. The way to build a dry building relies on your understanding and management of:
- Material science
- Quality assurance
RISK
Risk is about identifying weather exposure, the flood height of each area, movement (especially shrinkage and between different substrates), design issues (especially complicated joints or details), specifi c requirements of the manufacturer, any incompatible materials and use of best practice processes and products. High risk work such as posts/antennae or thresholds fixed through membrane, suspended pools, or ground level above internal levels needs to be properly detailed with input from all stakeholders, i.e. the designer, builder, subcontractor and manufacturer.
GRAVITY
Grade everything – substrate AND finishes – to drains. Lap and joint materials so moisture drains downhill. Fit overflows to any external area where flooding can occur.
MATERIAL SCIENCE
Forget water resistant. ALWAYS use waterproof membranes. Science has answers for most things. It tells us if a substance is unaffected if it is immersed in water. It tells us if a sealant is compatible with a liquid membrane. It tells us what depth and size of gravel to use to ballast a roof membrane. Most of the science is provided by the manufacturers.
Our job is to use this science to install a system where all the ingredients connect and blend without problems
QUALITY ASSURANCE (QA)
QA starts with your anaylsis of the contract documents. Is there anything that won’t work or will be very difficult to do? If there is, fix it by issuing an RFI setting out your concerns in writing. Then you need to: 1. Choose the correct waterproofing system.
- Ensure strict conformity with best practice.
– Manufacturer’s instructions, especially substrate, warnings, sequence and curing.
– All trades must respect and protect the system.
– Witness/inspection points are usually substrate, corner/joint detailing, after each coat and protection/barriers should be in place until finishes are completed. - Ensure all finishes are compatible.
- Obtain warranties and certification.
GETTING STARTED (OR WHAT I THINK THEY ALL MEAN)
I think the NCC and Australian Standards don’t intend to confuse us. So I will clarify a few things and try to translate their objectives.
As I see it, moisture is either water, water vapour or ice. Waterproof means moisture cannot travel through a substance or damage it. Water resistant means moisture cannot damage it.
The aim of the regulations is to tell us how to keep areas where moisture is present separate from other areas by what are really ‘tanks’ or impervious barriers called ‘membranes’ that permit moisture to drain, dry or do no harm.
Table 1 should remind you of what you already know. Part 2 of this article will provide added detail in the next edition. (N.B: I have drawn a line in the sand and condemned some of the silly practices that have and will continue to injure occupants or cause unnecessary call backs and repair costs.)